Crafting a Bespoke Wooden Lamp: A Comprehensive Guide This document provides a detailed guide to constructing a handcrafted wooden lamp, encompassing all stages from initial design considerations to final assembly and finishing. The project requires intermediate woodworking skills and familiarity with basic electrical wiring. Safety precautions are paramount throughout the process and should be strictly adhered to at all times. Phase 1: Design and Material Selection Defining the Lamp's Aesthetic Before commencing the construction, a thorough design process is crucial. Consider the overall style you wish to achieve. Will it be a minimalist, modern lamp, or a more rustic, traditional...
Sunday, February 2, 2025
Craft Your Own Lamp with These Woodworking Plans
Posted by
H Suhan
,
at
4:32 AM

Armoire Furniture Plans for Stylish and Efficient Storage Solutions
Posted by
H Suhan
,
at
12:36 AM
Armoire Furniture Plans for Stylish and Efficient Storage Solutions Transform your living space with a custom-built armoire! These versatile pieces offer a blend of stylish design and efficient storage, perfect for bedrooms, living rooms, or even home offices. Forget generic storage solutions; this article provides detailed plans and inspiration to craft an armoire that truly reflects your personal style and meets your specific storage needs. We'll guide you through the process, from initial design considerations to final assembly, ensuring a rewarding DIY project. Planning Your Armoire: Size, Style, and Function Before diving into the construction, careful planning is crucial. Consider...
Saturday, February 1, 2025
Design a Modern Woodworking Project with These Plans
Posted by
H Suhan
,
at
11:10 PM
Crafting a Modernist Coffee Table with Integrated Storage: A Comprehensive Guide This document details the design and construction of a contemporary coffee table featuring integrated storage, crafted primarily from sustainably sourced hardwood. The project emphasizes clean lines, minimalist aesthetics, and functionality, showcasing the beauty of natural wood grain while incorporating modern joinery techniques. The design aims for a piece that seamlessly blends with diverse interior styles, from mid-century modern to contemporary minimalist settings. I. Design Specifications and Material Selection A. Overall Dimensions and Proportions The coffee table will measure 48 inches in length, 24...
Barbie Furniture Plans for Crafting Tiny, Perfect-Scale Pieces
Posted by
H Suhan
,
at
10:54 PM
Barbie Furniture Plans for Crafting Tiny, Perfect-Scale Pieces Introduction: Embarking on a Miniature Crafting Journey The enduring appeal of Barbie dolls transcends generations, fueled by the imaginative possibilities they unlock. A significant aspect of this imaginative play is the creation of a meticulously detailed world, a miniature realm reflecting the larger human experience. This necessitates the crafting of exquisitely scaled furniture, a task that demands precision, patience, and a keen eye for detail. This comprehensive guide provides detailed plans for constructing a selection of Barbie-scale furniture pieces, empowering crafters of all skill levels to build a truly enchanting...
Saturday, January 25, 2025
DIY Wooden Wall Signs with Names or Quotes for Home Décor
Posted by
H Suhan
,
at
8:24 PM
Craft Your Dream Home: DIY Wooden Wall Signs Transform your house into a home with personalized charm using handcrafted wooden wall signs! This rewarding DIY project allows you to express your unique style and create meaningful décor that reflects your personality or commemorates special moments. Whether you’re a seasoned crafter or a complete beginner, creating a beautiful wooden sign is surprisingly accessible. This guide will walk you through the process, from selecting materials to adding the finishing touches, ensuring you create a piece you'll treasure for years to come. Gathering Your Supplies: A Foundation for Success Before you unleash your creativity, gather all the necessary...
Wednesday, November 20, 2024
How to Market and Sell Wood Toolbox Organizers
Posted by
H Suhan
,
at
7:56 PM
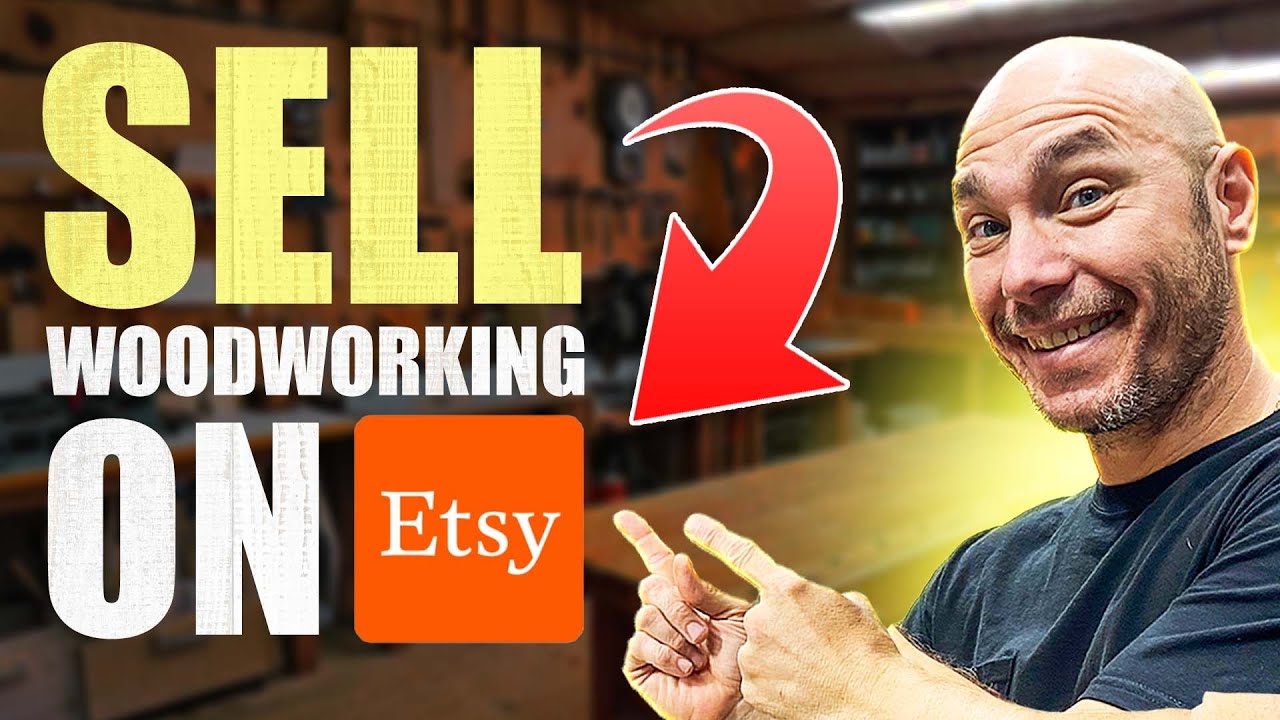
Marketing and Selling Wood Toolbox Organizers: A Practical Guide You've got the skills to make fantastic wood toolbox organizers, but are you struggling to get them in front of the right buyers? Don't worry, you're not alone! Marketing and selling handmade goods can feel like a whole new world. But with the right strategy, you can turn your passion into profit. This guide will break down everything you need to know about marketing and selling wood toolbox organizers, from understanding your target market to promoting your products online and offline. Understanding Your Target Market First things first, you need to understand who your ideal customer is. What kind of people are most...
DIY Tiered Plant Stands for Small-Space Living
Posted by
H Suhan
,
at
11:01 AM

DIY Tiered Plant Stands for Small-Space Living Transform your small space into a lush, verdant oasis with DIY tiered plant stands. These versatile structures allow you to showcase your beloved greenery while maximizing vertical space. You'll not only create a visually stunning display but also elevate your home decor with a touch of nature. Whether you prefer a rustic, modern, or minimalist aesthetic, the possibilities for customization are endless. Benefits of Tiered Plant Stands Tiered plant stands offer several advantages for small-space living: Maximize Vertical Space: Utilize unused wall space to create a vertical garden that adds life and color to your home. Versatile...
Subscribe to:
Posts (Atom)